Variations on dimensions without tolerance values are according to ' ISO 2768'. All tolerance limits are given in mm. ISO 2768 and derivative geometrical tolerance standards are intendedto simplify drawing specifications for mechanical tolerances. ISO 2768 is mainly for parts that are manufactured by way of machining or removal of materials. A hole dimensioned at 4 H7 may range from 4.00 - 4.012 mm, and a shaft at 4 h7 may range from 3.988 - 4.00 mm. Preferred tolerance classes and fits. ISO 286 identifies a set of preferred tolerance classes for holes which include G7, H7, JS7, K7, N7, P7, R7, S7, F8, H8, E9, H9, D10, A11, B11, C11, and H11. ISO 2768-1: General tolerances for linear and angular dimensions without individual tolerance indications. 3 All dimensions of machine parts prescribed in the production documentation should be specified using limit dimensions (tolerances) to avoid any uncertainty and dispute during production, checks and assembly.
According to DIN ISO 2768-1
According to DIN ISO 2768-2
General tolerances for linear measures and level squares with four tolerance classes are useful for simplifying drawings.
By choosing the tolerance class precision levels common in workshops should be taken into account.
If smaller tolerances are needed or bigger ones are more economical,
then these tolerances are indicated next to the nominal size.

Tabular 1 Limits for linear measures
Tolerance- class | Limits in mm for nominal sizes in mm | |||||||
0,5 to 3 | above | above 6 to 30 | above 30 to 120 | above 120 to 400 | above 400 | above 1000 | above 2000 | |
f (fine) | ± 0,05 | ± 0,05 | ± 0,1 | ± 0,15 | ± 0,2 | ± 0,3 | ± 0,5 | - |
m (medium) | ± 0,1 | ± 0,1 | ± 0,2 | ± 0,3 | ± 0,5 | ± 0,8 | ± 1,2 | ± 2 |
c (coarse) | ± 0,15 | ± 0,2 | ± 0,5 | ± 0,8 | ± 1,2 | ± 2 | ± 3 | ± 4 |
v (very coarce grob) | - | ± 0,5 | ± 1 | ± 1,5 | ± 2,5 | ± 4 | ± 6 | ± 8 |
For nominal sizes below 0,5 mm the limit measures are to be indicated directly at the nominal measure.

Tabular 2 Limit measures for radius of curvature and chamfer height
Tolerance class | Limits in mm for nominal sizes in mm | ||
0,5 to 3 | above 3 to 6 | above 6 | |
f (finne) | ± 0,2 | ± 0,5 | ± 1 |
m (medium) | |||
c (coarse) | ± 0,4 | ± 1 | ± 2 |
v (very coarse) |
Bei Nennmassen unter 0,5 mm sind die Grenzabmasse direkt am Nennmass anzugeben.
Tabelle 3 Grenzabmasse für Winkelmasse
Tolerance class | Limits in mm for nominal sizes in mm | ||||
to 10 | above 10 to 50 | above 50 to 120 | above 50 to 400 | above 400 | |
f (fine) | ± 1 ° | ± 30 ' | ± 20 ' | ± 10 ' | ± 5 ' |
m (medium) | |||||
c (coarse ) | ± 1 ° 30 ' | ± 1 ° | ± 30 ' | ± 15 ' | ± 10 ' |
v (very coarce) | ± 3 ° | ± 2 ° | ± 1 ° | ± 30 ' | ± 20 ' |
For nominal sizes below 0,5 mm the limit measures are to be indicated directly at the nominal measure. If general tolerances according to ISO 2768-1 are valid,
the following has to be inserted in the title box, i.e. for tolerance class medium
ISO 2768 – m or general tolerance ISO 2768 – m
For new designs only the general tolerance according to DIN ISO 2768-1 should be valid. The limit measurements of the tolerance classes m and f of DIN ISO 2768-1 are identic with those of DIN 7168-1.
According to DIN ISO 2768-2
DIN ISO 2768-2 is for simplifying drawing and fixes general tolerances in three tolerance classes for form and position.
By choosing a special tolerance class exactly the precision level common in workshops should be taken into account.
If smaller tolerances are needed or bigger are more economical these tolerances should be mentioned directly according to ISO 1101.
General tolerances for form and position should be used while the tolerance principle according. to ISO 8015 is valid and while this is mentioned in the drawing.
This tolerance principles says that no opposite relation between measure, form and position tolerance exists (principle of superposition).
Tolerance class | General tolerances for straightness and evenness in mm | |||||
Range of specified size in mm | ||||||
to 10 | above 10 to 30 | above 30 to 100 | above 100 to 300 | above 300 to 1000 | above 1000 to 3000 | |
H | 0,02 | 0,05 | 0,1 | 0,2 | 0,3 | 0,4 |
K | 0,05 | 0,1 | 0,2 | 0,4 | 0,6 | 0,8 |
L | 0,1 | 0,2 | 0,4 | 0,8 | 1,2 | 1,6 |
Tolerance class | General tolerances for straightness and evenness in mm | |||||
Range of specified size in mm | ||||||
to 100 | above 100 to 300 | above 300 to 1000 | above 1000 to 3000 | |||
H | 0,2 | 0,3 | 0,4 | 0,5 | ||
K | 0,4 | 0,6 | 0,8 | 1 | ||
L | 0,6 | 1 | 1,5 | 2 | ||
Tolerance class | General tolerances for symmetry | |||||
Range of specified size in mm | ||||||
to 100 | above 100 to 300 | above 300 to 1000 | above 1000 to 3000 | |||
H | 0,5 | |||||
K | 0,6 | 0,8 | 1 | |||
L | 0,6 | 1 | 1,5 | 2 |
General tolerances for form and position are valid for form elements for which form and position tolerances are not indicated individually.
They are applicable for all characteristics of the form elements accept cylinders, profiles of any line or surfaces, inclines, coaxiality, position and total movement.
Ramo AB ansvarar ej för eventuella felaktigheter i ovanstående information.
Ramo AB takes no responsibility in the eventuality of errors in the above information.
Relevant Standards
BS EN 20286-1:1993(ISO 286-1:1988 )...... ISO system of limits and fits. Bases of tolerances, deviations and fitsBS EN 20286-2 : 1993(ISO 286-2:1988 ).... ISO system of limits and fits. Tables of standard tolerance grades and limit deviations for holes and shafts
Notes
The tolerance of size is normally defined as the difference between the upper and lower dimensions.
The need for tolerances to be identified on drawings is vital to allow assembly of parts in the desiredway and interchangeability of parts as required in modern manufacturing methods.
ISO 286 implements 20 grades of accuracy to satisfy the requirements of different industries.
- IT01, IT0, IT1, IT2, IT3, IT4, IT5, IT6.. Production of gauges and instruments.
- IT 5, IT6, IT7, IT8, IT9, IT10, IT11, IT12...Precision and general Industry.
- IT11, IT14, IT15, IT16..Semi finished products
- IT16, IT17, IT18 ..Structural Engineering
Hole and Shaft tolerance tables- Using Fundamental Deviations and Tolerance Band T
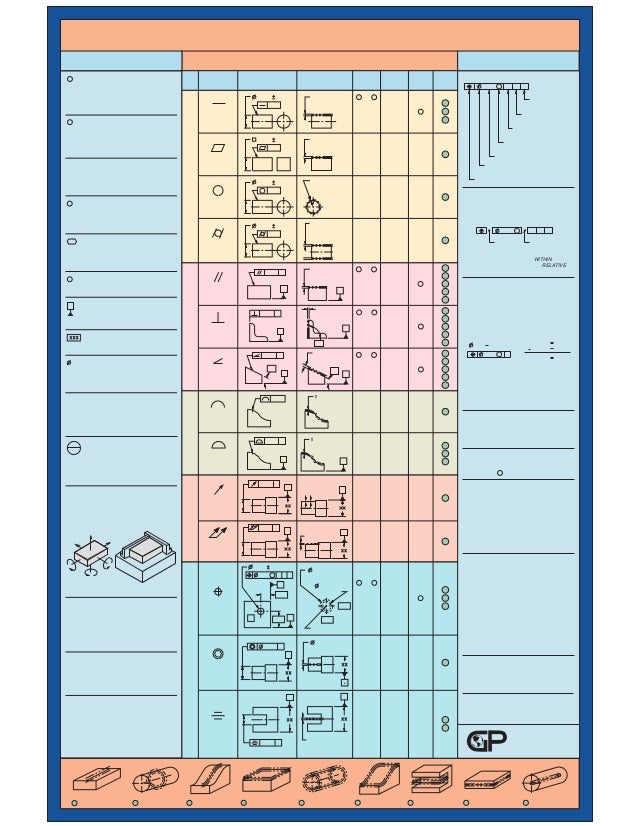
Iso 2768 Tolerances
ISO Tolerance Band T (3-315mm size) | ISO Shaft limit nearest Zero (3-500mm shaft size) | ISO Hole Nearest limit nearest Zero (0-500mm hole size) |
ISO Tolerance Band T (315-3150mm size) | ISO Shaft limit nearest Zero (500-3150mm shaft size) | ISO Hole Nearest limit nearest Zero (500-3150mm hole size) |
Examples in using above tables..
Note: The tolerance band T is an absolute length value it does not have a negative value.
Hole Dia 110mm H11,...
Nearest zero ( El )= 110mm + 0mm = 110,000mm ...
Furthest from zero ( ES )= 110mm + (0+ T=0,220)=110,220mm
Resulting limits 110,000/110,220
Shaft 110mm e9...
Nearest zero ( es ) = 110mm - 0,072=109,928mm...
Furthest from zero ( ei ) = 110mm - (0,072 + T=0,087) = 109,841mm
Resulting limits 109,928/109,841
Note for the tolerance bands which can be either side of zero, (J,K,N,j )
The diagramsprovided with the table clearly show calculation needed.e.g. consider Hole 300K7.
T= 52 micrometres (0,052mm).Limit nearest zero ( K ) ES = 16 micrometres = (0,016mm)
Limit furthest from zero ( K ) El = (0,016- 0,052)= -0,036
Limits therefore (300 -0,036) = 299,964..and ...300+0,016= 300,016
limits 299,964/300,016
Iso 2768 Hole Tolerance It6
Hole and Shaft Tolerances to ISO 286-2ISO Hole Limits (3-400mm Hole Size) | ISO Shaft Tolerance(3-400mm Hole Size) |
ISO Hole Limits (400-3150mm Hole Size) | ISO Shaft Tolerance(400-3150 mm Hole Size) |
Example limits and fits using hole basis
Description | Hole | Shaft |
Loose Running | H11 | c11 |
Free Running | H9 | d9 |
Loose Running | H11 | c11 |
Easy Running - Good quality easy to do- | H8 | f8 |
Sliding | H7 | g6 |
Close Clearance - Spigots and locations | H8 | f7 |
Location/Clearance | H7 | h6 |
Location- slight interference | H7 | k6 |
Location/Transition | H7 | n6 |
Location/Interference- Press fit which can be separated | H7 | p6 |
Medium Drive | H7 | s6 |
Force | H7 | u6 |
Machining Process associated with ISO IT Tolerance Grade..
Iso 2768 Hole Tolerance
IT Grade | 2 | 3 | 4 | 5 | 6 | 7 | 8 | 9 | 10 | 11 | 12 | 13 | 14 | 15 | 16 |
Lapping | |||||||||||||||
Honing | |||||||||||||||
Superfinishing | |||||||||||||||
Cylinderical grinding | |||||||||||||||
Diamond turning | |||||||||||||||
Plan grinding | |||||||||||||||
Broaching | |||||||||||||||
Reaming | |||||||||||||||
Boring, Turning | |||||||||||||||
Sawing | |||||||||||||||
Milling | |||||||||||||||
Planing, Shaping | |||||||||||||||
Extruding | |||||||||||||||
Cold Rolling, Drawing | |||||||||||||||
Drilling | |||||||||||||||
Die Casting | |||||||||||||||
Forging | |||||||||||||||
Sand Casting | |||||||||||||||
Hot rolling, Flame cutting |